連載・トロコイド加工(マパールからの発信)3回目(最終)
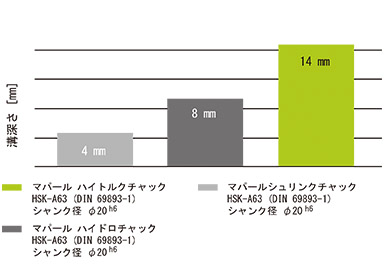
図6 ツールホルダーの違いによる最大加工溝深さ sorce Mapal.
3. 工具とコーティング
トロコイド加工の潜在能力を発揮し最大限に活用するために、工具の選定は加工仕様に適合させなければならない。刃先の工具材種を適切に選定するには、高性能なコーティングや被加工物の適応した刃先形状もまた重要である。工具素材に関しては、特に引っ張り強さや刃先強度が極めて重要な特性である。一方、衝撃力や耐熱衝撃性はそれほど重要ではない。これらの特定の要求品質を満足するため、マパールは微粒子あるいは超微粒子の超硬素材を使用している。
加工ワーク材質に応じて、工具材種はコバルト含有量8―10%の超硬が使用される。硬さを最大化あるいは摩擦力を最小化するため、これらの超硬素材と高硬度の複合コーティング層を最適に組み合わせて使用する。あらためて図5にこのツーリングシステムに関する必要特性をまとめて示す。さらに不等切れ刃の採用は工具の振動抑制に対して有効である。しかしながら工程に採用される高速加工条件下では、不等切れ刃により生じたアンバランスは加工性に悪い影響をもたらす。当初の対策として、アンバランスはバランスチャックの使用により解決された。
すなわち加工速度の上昇にもかかわらず、表面粗さ、加工品質の向上、および摩耗の抑制が達成できた。その後、さらに先進的なアプローチとして工具の設計時点でバランスの改善を実施した。コンピュータシュミレーションによるアプローチにより、突き出し長さのそれぞれの位置でアンバランスが最小となるように工具の断面形状を選定した。工具形状を最適化する繰り返しループのアルゴリズムにより工具のアンバランスを最小化させた。
最適にバランス調整された不等分割工具は、特殊タービンブレードいわゆるブリスク(Blisk:ブレード+ディスク一体成形)の生産に頻繁に使用される。ブリスクはブレードとディスクを接合し一体化した構造から成っている。専門家の見解調査によると、ブリスクの需要は2020年までに少なくとも2倍になると見積もられている。古くからのブレードとローダの接続による取り付け方法と比較して、ブリスクはコンポーネントの重量を軽減すると同時に、コンパクトで極めて高い性能を得ることができる。
しかしながら一体型ブリスクの生産は、非常に複雑でコストがかかり、不良品となるリスクが高くなることが問題となっていた。ブリスクは薄肉構造のため、高能率で安定した加工プロセスを実現するには、可能な限り低い振動条件で加工が行われる必要がある。ハイトルクチャック(HTC)の概念はこのような要求を配慮し、工具のクランプと振動減衰の両方の効果を兼ね備える。このハイドロチャックによる加工時の働きは、たとえば溝加工において明らかである。ほかのチャックと比較して、スロットを大幅に深くしてもプロセスは安定している(図6)。その結果、得られる効果として加工条件を上げ、加工時間の短縮が実現し、切れ刃エッジのチッピングが抑制される。
4. コスト削減の潜在的可能性
マパールの研究報告では、トロコイド加工の採用による工程の合理化事例について述べられている。ここでは肌焼鋼16MnCr5とステンレス鋼SUS304の薄肉構造ワークの加工が比較されている(図7)。
従来の肌焼鋼のドライ加工における切削速度(Vc=140~240m/min)に対してトロコイド加工では約3倍の切削速度で加工が可能となり、同時に1刃当たりの送り量を2倍(fz=0・1㎜)まで上げることができた。また切削条件で注目すべき特徴として、マパールエンドミルは深さ3Dまでの加工に対応することが挙げられる。このように工具への加工負荷の軽減と摩耗の低減を同時に達成し、全体の加工時間の短縮を実現した。トロコイド加工によって、次の3つのプラスの効果が得られた。すなわち加工時間の短縮と工具寿命の延長に加え、費用効果の高い小径工具の使用が可能となった。
トロコイド加工が成立するための前提として、ツールパスを最適化するCAMソフトウェアが必要となる。ソリッドワークス(SolidWorks)に組み込まれたCAMソフトウェア‘iMachining’を使用すると、加工ワーク材質、工具形状および加工マシンから最適な切削パラメーターが導き出される。CAMソフトウェアにより、現状保有している設備においてもより効率的な加工が可能になる。
実際の加工事例として、幅32㎜×深さ8㎜の溝加工で、φ16の超硬ソリッドエンドミルを用い、切りくず排出量が65%増加した。
トロコイド加工による大幅な生産性の増加は、量産加工ラインでも実現可能である。たとえば、エンジン製造工程の事例では、チタン合金Ti6242の加工工程で工具コストはおよそ50%削減された。ニッケル基合金やインコネル718の加工においても、大幅なコスト削減が可能である。溝加工の事例では加工時間を63%、工具必要数量を72%、工具コストを61%削減した。
また、計測機器の構造部品の加工工程の事例を以下に示す。この加工工程は高い切りくず排出量、ワンクランプでステンレス(X17CrNi16‐2、JIS:SUS431)の削り出し加工が特徴となる。この加工の場合、トロコイド加工の導入により、加工時間は以前と比較しておよそ70%削減された。これらの良好な結果を踏まえて、この会社では今後も別の業種の加工分野、たとえば微細加工などにもトロコイド加工を活用する方針を示している。
5. おわりに
航空宇宙産業や自動車業界などの多くの部門で、さまざまな技術的要件を満たす部品のニーズが高まるとともに、チタンやニッケル基合金のような耐熱性の高い材料がますます多く使用される。これらの難削材料の加工は工具やマシンの選定にとって大きな課題となる。生産性を確保するため、要求された加工条件に最適な工具、マシンおよび工程を選定しなければならない。しかしながら、これまで一般的に実施されてきた全幅加工は大きな加工負荷が生じ、また工具の摩耗が急速に進行する。トロコイド加工は切りくず排出量を増加させ、一方では加工負荷を軽減させる有効な加工方法である。
工具の円弧軌道と送り運動のオーバーラップにより、切れ刃とワークの接触条件が改善される。使用工具や溝幅の違いによってきめられた接触条件の下で、ツールパスに沿って周期的な加工が行われる。このようなトロコイド加工の採用により切削幅および切削長さが減少し、加工負荷および工具摩耗は大幅に低減される。このように全幅加工ではおおよそ1×Dに制限されている溝加工が、トロコイド加工では2・5×Dを超える切削深さの加工が可能となる。
またトロコイド加工では、極めて高速切削が可能となることが挙げられる。さらに切削長および溝幅は工具径の制限を受けず、工具の有効利用が可能となる。その結果、幅広い範囲の幅の異なる溝を1本の工具で加工することができ、生産の効率を向上させることができる。トロコイド加工に対して最適となるように特別に設定された工具、チャック及びツールパスを使用することで、ますますトロコイド加工の効率化を図ることができる。このようなトロコイド加工の特性により、深溝加工や深堀り加工部品の加工効率は大幅に向上する。トロコイド加工の効果は、実際の量産加工の現場で確認されており、トロコイド加工をほかの業種あるいは加工プロセスに広めることにより、多くのアプリケーションで、加工時間、工具コストおよび使用工具数量を大幅に削減することが可能になる。
図5 トロコイド加工におけるツール材料の影響 sorce Mapal
図7 マパールトロコイドエンドミルによる薄肉構造ワークの加工条件