ビビリ音解消にユキワ精工ツーリングを採用し、
解決したヤマト(長野県・上諏訪)
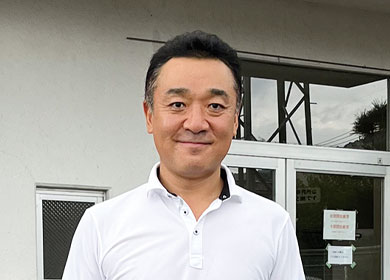
取材に応じてくれた渡辺社長
ヤマトは、ビデオデッキ関連の組み立て工場として1964年に創業したが、その後、部品加工にも乗り出し業容の拡大を追求するとともに、マシニングセンタを上手く活用して付加価値の創造を試みてきた。たとえば、他社では1工程で対応できなかった加工を、治具で工夫することにより可能にした、といった例などが挙げられようか。
2003年入社で、2代目を継いだ渡辺高志社長は「今では取引社数およそ200社。精密切削加工が8割以上を占め、残りはプラスチック成形、組み立てで、ほとんどが長野県外からの仕事。リピート率は70%にのぼる」魅力ある企業に発展しているが「2008年に発生したリーマンショックが当社の大きな転換点。翌年の売り上げでは60%以上が消失した」そうだ。
ヤマトの生産拠点は、本社のある上諏訪工場と、歩いて数分にある、下諏訪工場の2カ所から成り、リーマンショックからの脱却として「カム式の機械を処分し、主力の自動盤を上諏訪工場に集約して、下諏訪工場を空にしてスペースを確保。最新鋭の設備導入と仕事の受注が噛み合うような展開を模索していった」。
仕事の確保では、毎年のように設備投資を行う一方、展示会も積極的に活用し、ネプコンジャパンや機械要素展などに出展、営業的な成果を展望した。
マシニングセンタを駆使する下諏訪工場には、オークマ1台、ブラザー工業3台、滝沢鉄工所4台、静岡鉄工1台など計16台が稼働している。9月には老朽化の更新として、ファナックのロボドリルが導入予定だ。このほか、下諏訪工場には、円筒や平面の研磨機、ホブ盤、ブローチ盤、ワイヤカットなどを設備している。
特にマシニングセンタについては、最新鋭にこだわりつつ、機械剛性と回転速度を意識すると言う。
「スーパーG1チャックを勧めてくれたのは、お付き合いのある商社の営業マンの方。2017年ころだったと思うが、キーシードカッタを駆使した加工で、ビビリ音が半端なく大きく、相談に乗ってもらったのが始まりだった」と言う。
他社のツーリングからスーパーG1チャックに付け替えると、直ぐに成果となって表れた。
「騒音とも言えるビビリ音がなくなり、静かになり、刃物の寿命が伸びて、工具1本当たりの生産個数が2倍となったうえ、夜間運転まで可能になった」。
1ロット100個から200個が多いが、1個、2個の試作もあり、1000個以上のケースもある。受注量が拡大していくなか、現在の3直24時間フル稼働を可能にしたのが、スーパーG1チャックだったと言い換えることもできるだろうか。スーパーG1チャックは、8本所有するまでになっている。
「今後もツールホルダの更新時に拡充していく計画」だと言う。
ビビリ音が解消したと語るオペレーターの内藤さん
下諏訪工場の様子