電着砥石に替えて時計外装部品加工を協和精工製PCD工具でテスト。加工時間短縮、良好な仕上がり面などを享受したOrbray。
今後はドリル、エンドミル採用を検討へ
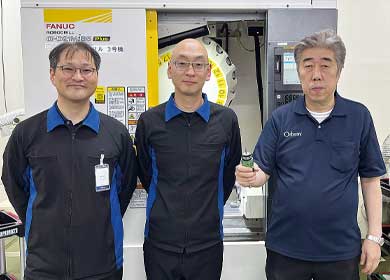
取材に応じてくれた村上本部長(中央)濱倉係長(左)とオペレーターの畠山さん
多様な事業部門を抱えるなかで、本紙が今回、お邪魔したのは秋田・湯沢市にあるOrbray[TRAD]と呼ばれる、腕時計の外装部品とレコード針の製造を担う拠点。月に一度の割合で市民コンサートが開かれるほど湯沢市は「音楽の街」として知られているようで、アナログ音源(レコード針)の担い手として、Orbrayは運営にも協力を惜しまない。事前にレコード針はダイヤモンド製と聞き、協和精工製PCD工具が、この分野でも活かされていると想像していたが、協和精工のもうひとつの「顔」である、腕時計部門で成果を上げつつあった。
◆
応対頂いたのは、精密宝石事業統括の村上第一製造本部長と濱倉加工技術係長。
「腕時計のケースをはじめとする外装部品は、欧州高級腕時計メーカーからの受注。時代の変遷に伴い、被削材が超硬からセラミックス(ジルコニア)へと移行するなかで、弊社の得意とする『切る、削る、磨く』技術をブラッシュアップさせながら、特に電着砥石の活用を軸に対応してきた」。
協和精工との出会いは、Orbrayに社名変更される並木精密宝石時代からだったが、暫く往来がなく、たまたま、昨年開催された展示会で、ブースが隣り合わせとなり「再会」を果たしたと言う。
「共通の商社とお付き合いがあったこともあり、半年前に同行PRで弊社を訪問頂き、協和精工さんのPCD工具をテストする機会を得た」。
協和精工から勧められたのはPCDエンドミルとPCDドリル。当初、切削工具は外装部品加工では使えないと思っていたそうで、当然ではあるが、電着砥石とは違う(切削)条件出しというトライアルが伴った。
「PCDエンドミルはジルコニアで荒加工テストを実施。従来の電着砥石に比べ、加工時間が半分。仕上がり面もきれいで、ピン角も作りやすい。一方、PCDドリルは石英ガラスで穴開けテストを実施。どの条件でも仕上がりは現在使用しているメタルボンドダイヤモンドツールと同等で、送り速度を上げても問題なく、加工時間も半減。ドリルによる一発仕上げでも仕上がりは他の条件と大差がなく、小径の穴を大量に開ける製品には加工時間短縮に直結する」という結果を経て「電着砥石をベースとした技術から、ツールを選ぶ選択肢が増えたことで、どのような可能性があるか、もっと探っていきたいと思う」段階へと移ってきている。
今回テストしたのがDSRのφ3ミリとφ2ミリ。この工具は刃数が6枚刃という高能率用に協和精工が開発したPCDエンドミル。ドリルはオーダーメイドだそうだ。
Orbrayでは、腕時計の外装部品加工は、月当たり200個レベル。電着砥石からPCD工具へのリプレースがどこまで進むか。荒加工ばかりか、中・仕上げの工程でも、アプリケーション技術を獲得しつつ、挑戦していくことを期待しない訳にはいかない。
電着砥石からPCD工具へのリプレースはどこまで進むのか
ロボドリルに装填し、時短と仕上がりの面の綺麗さが追求される