ワークハンドリングホルダを自社のキーレスチャック加工現場に適用しているユキワ精工 夜間の無人運転で効果を発揮
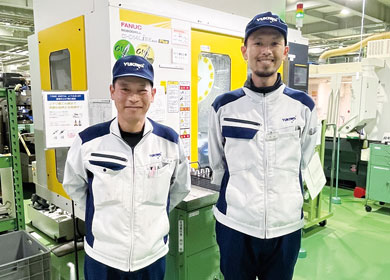
キーレス製造グループマネージャーの吉原さん(左)とオペレーターの内山さん
人手不足への対応としてユキワ精工が提唱している「ワークハンドリングホルダ」。ロボットの代わりにツールホルダでワークを自動で交換する有力ツールとして注目を集めているが、昨年来から自社工場内でも活用し、成果を上げている。4月号では本社小千谷工場を訪問し、オペレーターに効用を具体的にヒアリングしながら、紙面化を図ってみた。
ワークハンドリングホルダが活用されているのは、月産500個~600個に及ぶキーレスチャックの製造現場で、担当しているのは、内山スタッフだ。
「チャックの開閉時に3本の爪を支えるガイド(S45C)の部品加工で、2023年に導入したワイド仕様のロボドリルに適用した。従来、ガイド加工は、手付機(汎用機)3台で行っていたが、これをリプレース。治具の簡素化も図れるようになった」そうで「パレットに加工ワークをセットアップし、ワークハンドリングホルダで掴んで搬送した後は、スーパーG1チャックで穴あけ(ドリル加工)、グリーンG1チャックで横引き(エンドミル加工)を行い、仕上げていく流れとなる」。
ガイドの大きさにもよるが、最大で2パレット96個分に対応すると言う。
「ワークハンドリングホルダを活用した1パレット分の仕事量に相当する6時間~6時間半が、人が関わらなくともいい時間として確保でき、他の仕事に振り向けられるようになった」。
帰社するときに夜間運転の準備を済ませれば、人が介在しなくても、加工を終えることができる。たとえ、夜間で問題が発生しても、自動的に停止するので、心配はないそうだ。
酒巻社長は「ワークハンドリングホルダは昼間での効率化、省人化に寄与するが、特に、働き方改革にも通じる、夜間運転での活用を訴えたい。特にワークが小さい場合は、パレットへの並べ方に工夫を凝らしていけば、想像以上に効率化が図れると思う」と、小さな部品加工を行っているユーザーへのアピールを意識する。
ワークハンドリングホルダは外径把握用と内径把握用の2種類があるが、いずれも30番主軸仕様。今後は40番仕様にも注力していくそうだ。
「治具メーカーとの連携も大切。弊社でも紹介しており、問い合わせいただければ」と酒巻社長は訴える。
営業スタッフによる顧客訪問は重要だが、一方で限界があるのも事実。「使用上で、分かりやすい動画を作成して、アピールしていく必要性を感じている」(酒巻社長)。
ワークハンドリングホルダで、ガイドを掴んで運ぶ。無人化に直接寄与していく