日産自動車追浜工場・第一圧型製作課におけるユキワ精工製「スーパーG1チャック」評価
荒取り加工における「ビビリ=あおられ」発生を従来比10分の1に抑制、工具寿命も2倍のイメージ」
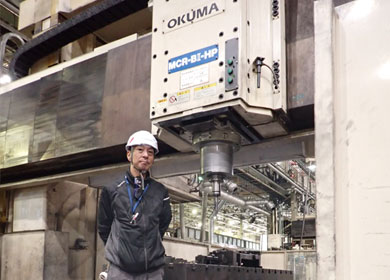
取材に対応いただいた住吉専門工長
日産自動車追浜工場は、東京ドーム36個分という広大な敷地を擁する、車体製造の一翼担う拠点工場だが、今回、訪問したのはその敷地内に位置するプレス型の生産拠点だ。
「我々の所属部署では、完成車の部品を生産する金型の生産を担当。求められる公差は100分の3。手がけているのはボディーサイドで、型サイズでは4mを超え、型重量では30トンを超える。現場はFMSラインが構築されており、各部品・部材の運搬には、AGVが多用され、自動化を追求している。型製作の流れは、機械加工に始まり、組付け、プレスを経て、型修正・完成後、各拠点の生産工場に出荷されて量産準備に入っていく」と説明する。
工程集約の観点から、ワークの一体化シフトが進んで、型の大型化が進行。併せてパネル材はアルミが増えてきている。
「現場は2直体制。機械設備は、カスタマイズされたオークマ製(50番主軸)MCR‐B2とMCR‐Sが大半を占めている。これは同社独自のOSPというCNC制御装置がとても扱いやすいという理由からだ」。
余談になるが、自前で切削工具を製造している点も、この現場の特徴で、工具研削盤ではワルター製ラプターが稼働している。
さて、ユキワ精工のツーリングとの出会いであるが、2022年に、その伏線となる事態に遭遇。スピード勝負の荒取り加工で「ビビリ=あおられ」が発生し、どう対処していくかが問われたからで、その一案としてツールホルダの変更案が浮上した。
「翌年の2023年2月にオークマの北関東カスタマーセンターを訪問する機会があり、その時、ユキワ精工の方に初めてお会いした。早速、荒取り加工時のビビリ発生で相談したところ、スーパーG1チャックを勧められ、テスト加工を実施することになった」。
もちろん、テスト加工はツーリングだけ変更し、あとの切削条件は同じ。
「荒取り加工時は厳しい切削条件を設定しているが、スーパーG1チャックを装着することで、切削工具のあおられの発生が従来比10分1に抑えられた。その結果からの感触だが、工具寿命は2倍に伸びるイメージを抱いた」そうだ。
その後、径10ミリの工具を掴む、荒取り加工用として、スーパーG1チャックを「必要最低限」に当たる70本購入した。
「荒取り加工で結果が出たので、次は減衰性能で期待をしているグリーンG1チャックにトライしたい。すでに挙がっている案件だが、径6ミリ、30Dのロングドリルによる自動化計画で活かしていければと思っている」。
昨年5月にはユキワ精工本社・工場を訪問した。
「サイズ拡充に期待しつつ、ツーリング寿命の判定基準は?その点検方法は?といった質問やお願いをさせて頂いた」。
ツーリングで加工が変わる‐日産追浜工場でも有力事例を紹介いただいた。
大型プレス金型の生産拠点