切削加工軸に多様な産業で成果。被削材の広がりで「グリーンG1チャック」の有効さを検証。「刃持ちが2倍近くに」品質保証では検査員を配置している。
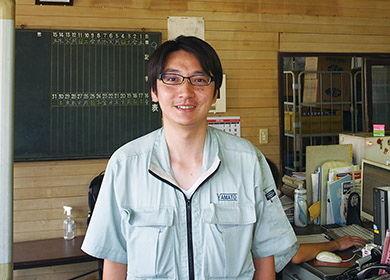
福岡弘義社長
リーマンショックで転機を迎えた企業は多い。岩手・北上市で、主に自動車や商用車、農機具、半導体製造装置といった各部品の切削加工業を営む大和製作所も例外ではない。
「2008年、リーマンショックが発生した時点で主要な取引先が12社~16社。その後、負の振れ幅が大きくなるにつれ、各社からの受注量が激減。開拓の必要に迫られた」と福岡弘義社長は言う。
1993年からリーマンショックまでの、およそ15年間、大和製作所は、売り上げの9割を占めるほど、アルミダイカストの2次加工(切削加工)に特化した時代が続いていた。ロットで2万個というのも珍しくなかったようだ。
「(受注量の激減で)各社の協力会を歩き仕事を紹介してもらう中で『素形材の分野だけでは範囲が狭いのではないか』との知人からのアドバイスがあり、紹介を受けるなかで、半導体製造装置メーカーの下請けからの仕事を頂くようになったが、これが大きな転機となった」。
従来、同社であまり加工していなかった鉄やステンレスの加工に挑むことになる。
「ユキワ製グリーンG1チャックとの出会いは、3年ほど前から急激に増え始めた半導体製造装置関連部品のステンレス加工で、まったく刃持ちしないと言う事態に直面し、思案した末、その解決策をツーリングに求めようとしていた時期と重なり合う。商社の方に何かいいツーリングがあれば持ってきて、と頼んで紹介された」と言う。
大和製作所の現場には、20台以上のブラザー工業のタッピングセンタ(30番主軸)が据えられている。振動を抑え、刃持ちを良くする手立てとして剛性の高い主軸40番で、との選択肢ではなく、ツーリングに打開を求めたことになろうか。
オペレーターの千葉さんによると「受注は100個単位と、まとまったロット数だけに、消耗品である工具の寿命は気になるところ。従来のツーリングでは、4個かせいぜい5個加工した時点で、刃が持たなかったが、グリーンG1チャック導入後は7個までカバーできるようになった」そうだ。
30番主軸の剛性面でのフォロー、ビビリ抑制について、グリーンG1チャックがヒットした好例だろうか。
「ステンレス加工で効果が実感できたので、振動の状況や刃物の状態を確認しながら、他の被削材の加工や、昨年、ものづくり補助金で購入したOKK製40番主軸のVC‐X350でも採用するようになってきた。今後、ユキワ製スーパーG1チャックの導入も図り、棲み分けしたいと考えている」。
設備に対する考え方として福岡社長は「基本的には汎用機は維持し続けたい。特急対応に不可欠であり、技術的向上にも繋がる。マシニングセンタなら5軸加工機、旋盤なら複合機を選択したい」。
取引先は40社程度にまで拡大、うちコアとなるのが4社だが、リスクを軽減していくうえでも、1社の売り上げに占める割合は、大きくても20%程度にとどめたいと言う。
「売り上げの数パーセントが紹介の紹介で成り立っている」というエピソードも福岡社長は語ってくれた。人間関係の力は大きい。 3次元測定機や粗さ・形状の各測定機ばかりか、専任の検査員も配置しており、品質保証に抜かりはない。
「私の祖父が創業し、私で3代目になる」という福岡社長は、リーマンショック前に入社し、景気の振幅の「激震」を経験した。まだ、37歳という若さだが、経験の密度は濃い。
昨年導入したOKKのマシニングセンタでもグリーンG1チャックの性能が試されている
切削加工の技術ノウハウを補完する豊富な設備群