設備先行で受注確保するKb・Spirit(岩手県・一関市)-ユキワ精工ユーザー-訪問
「テスト結果ではビビリが大幅に抑制され、刃持ちは2倍以上」加藤社長に聞く
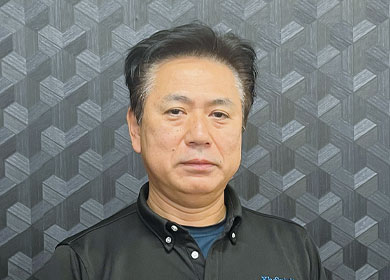
加藤社長
25年間、勤務した会社を7年前に受け継いで、責任者となって新たなスタートを切った加藤社長は「この間、人脈を活かしたネットワーク網の構築を通じ、業績が軌道に乗っていくなか、工場拡張を視野に入れて2年前に現在地に移転、同時に社名をKb・Spiritに変更した」との経緯を語る。
大手電機メーカーからのコネクタ・部品関連の仕事が6割を占め、その他10社から請けるモータ部品や空圧部品、ダイキャスト製品等で4割を占める。設備では、前者はシチズンやミヤノなどの自動盤が中心で、後者はファナックのロボドリルを核とするマシニングセンタが活躍する。
「新たにスタートを切った7年前に、取引商社の勧めでロボドリルにユキワ精工製ツーリングを導入した。採用を決定づけたのは、精度の高さとチャッキングの汎用性の高さの2点だった」そうで、その際、空圧部品の加工で他社製ツーリングとグリーンG1チャックの比較テストを実施した。
「テスト結果では、ビビリが大幅に抑制され、刃持ちは2倍以上の長寿命化を達成した」。
ロボドリルで手がける部品加工は1ロット2000個から3000個。被削材はステンレスやアルミダイキャストが多い。
ロボドリルのオペレーターである加藤修幸さんによると「現在、スーパーG1チャック14本、グリーンG1チャック5本を活用している」そうで「粗加工と言った加工の場合はスーパーG1チャック、加工精度の高い加工の場合はグリーンG1チャックと、使い分けしている」と言う。
振れ精度の高さによって面精度を確保し、工具寿命の点で「高剛性」といった利点を、切削条件を上げても工具寿命が良いといった効用を生んでいる。
今年の5月にはロボドリルを新たに設備して、総計3台が現場に据えられた。
加藤社長は「仕事が入ってきたから設備するのではなく、仕事を受注していくために設備を充実させていくと言う考え方。弊社ではマシニングセンタばかりか、自動盤でも、ユキワ精工製のEYツーリングを活用しており、今後も活用の幅は広がっていくと思う」と期待を寄せる。因みに円テーブルもユキワ精工製!惚れこみようが徹底している。
マシニングセンタはロボドリルを核に設備している
高剛性なビビリ耐性と評価する加藤オペレーター
ツーリングばかりか円テーブルもユキワ精工製だ