ユキワ精工製グリーンG1チャックでビビリ解消したナツメ(豊橋市)の銅電極加工。刃持ちも2倍以上に
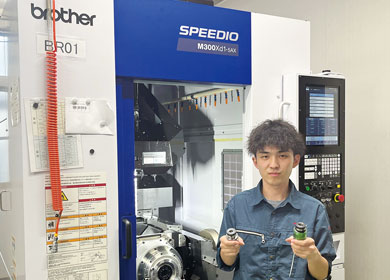
初導入となった5軸加工機、スピーディオにも、すでにユキワ精工製ツーリングが20本に
スポット溶接で使用される銅電極の加工が8割を占めるナツメを訪問した。
創業は1968年、織機などの部品加工でスタートしたが、1980年代以降、大手溶材商社との付き合いが深まるなか、溶接機メーカーとも信頼関係を築いていき、順次、取引が拡大、銅電極加工が社業の柱となっていったそうだ。
夏目社長は「現会長の私の父が豊川市で創業した。現在、取引企業は300社ほどを数えるが、そもそも大手溶材商社との出会いがなければ、今の弊社はない。スポット溶接機のユーザーと言えば、自動車関連の現場が多い」と語る。
銅と言っても加工で使用されるのは、クロムが加えられ、HRB70まで硬度が上げられたクロム銅になると言う。
「常態の銅ではHRB30程度と、硬度が低いうえ、粘りが高く、比重も高いという特性をもっており、加工上、刃持ちが悪く、仕上げの難しさに直結するほか、応力への対応、キズへの配慮など、取り扱いには、神経を使う」と言う。扱いづらい材料の好例だろう。
取扱量は月間60万個という、半端ない加工総量に達する。
電極は、キャップチップに代表される量産モノが3割を占め旋削加工で対応。旋盤1台当たり2000個/日程度をこなす。NC旋盤は30台、汎用旋盤10台を数える。
キャップチップなどに取り付けられる土台が残り7割に相当し、単品モノ、小ロット(10個程度)が占めており、その一部はマシニングセンタで加工していく。
「毎月、現場では3000件、2000種類に及ぶ部品が流れている。図面付きで指示書が回ってくるなか、作業従事者50人で、納期は2週間目途で対応している」そうだ。
ユキワ精工のツーリング、グリーンG1チャックが導入されたのが昨年の7月。
「ロボドリルで手がけていた銅電極のベース加工で、ビビリが多く発生し、困っていたところ、商社からの勧めもあって、ユキワ精工さんからサンプルを出していただき、従来のツーリングに替えてテスト加工を実施。ビビリが大幅に軽減したばかりか、切削条件を上げてもほとんどビビリが発生しなくなり、稼働率が向上。さらに刃持ちの点でも2倍以上となり、ツーリングはユキワ精工、との思いを強くした」そうだ。
今年の6月にはロボドリルの老朽化更新に合わせ、ツーリングはすべてユキワ精工を選択。グリーンG1チャックとスーパーG1チャック併せて28本導入。
「また、銅電極加工を5軸加工でトライし、経験値を築いていこうとの考えから、同時期にブラザー工業製スピーディオの5軸加工機を現場に据え、ユキワ精工製ツーリング20本を装着した」。
2台の新規設備にスーパーG1チャックとグリーンG1チャック、総計48本が活用されることになったが「高速仕様の場合はグリーンG1チャック、精度重視ならスーパーG1チャックを選定している」。
最後に夏目社長はメーカーへの要望として「弊社での5軸加工機での経験値を積んでいくことにも関わるが、突き出し量が長くなる加工であっても、ビビらずに加工ができる、そんなツーリングの提供を期待したい」と語った。
最新のロボドリル(本社工場)にはユキワ精工製ツーリングが合計28本がセットされている
グリーンG1チャックを装着し、ロボドリルでテスト加工を実施