営業スタッフ充実で、リピート顧客のフォローと新規開拓 突出し量の長い加工、大径加工でスーパーG1チャックを選択した博洋エンジニアリング(東大阪市)
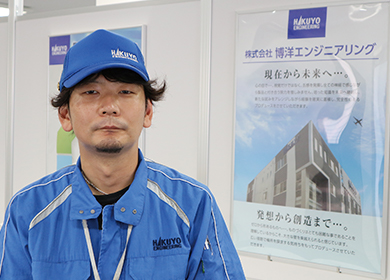
この道23年になる塚本工場長
- 2020年で創業30周年という節目を迎え、今期(12月決算)は「過去最高の業績がすでに見えている」博洋エンジニアリングを訪問する機会を得た。23年のキャリアを持つ塚本工場長との面談ばかりか、業務の豊田課長も紹介されて「当社は57人中、11人の営業スタッフを抱え、既存顧客のフォローと新規開拓に従事している」との部品加工業では珍しい「攻め」の体制について、冒頭で説明を受けた。
- 現状の仕事は半導体関連が7割とメインで、他にEVのリチウムバッテリーの部品加工とアッセンブリー、携帯電話やタイヤ内にセットされる電池部品などで構成される。
- 「半導体分野は、半導体製造装置のシール部品や搬送用のレール関連、一部にアッセンブリーも手掛けている。また、リチウムバッテリー関連は、ほとんど需要が消し飛んだ航空機分野に代わり、営業の成果として、昨年から請け負い始め、1日15台ペースで製作、まだ、1年も経っていないのに4000台レベルの納入実績が積み上がってきた、急成長分野だ」そうだ。
- 製造では、プログラミングに始まり、機械のセッティング準備、刃物の選定、治工具や材料の段取りから仕上げまでの一貫した対応に心血を注ぐ。
- 塚本工場長は「基本的に図面付きで指示が回ってくる。単品ものもあるが、1ロットで見れば、およそ100個程度が大半。毎日、段取り替えが、どこかの機械で行われている」。
- 機械設備については、切りくず排出性の良さや剛性の高さをはじめ、故障の少なさ、繰り返し精度の高さなどを重視。制御装置はファナックに統一している。
- 「ユキワ精工さんとの出会いは、半導体製造装置関連の400角のアルミ構造部品の仕事が舞い込んできた、2年ちょっと前くらいになる。加工上、刃物の突出し量を長くすることが求められたが、従来のツーリングではビビってしまい、販売店に相談したところ、スーパーG1チャックを勧められた」そうだ。
- デモ機を手に取った塚本工場長の感想は「遊びがなく、均等に締まっている」。
- 実際に試してみると「従来のツーリングでは、どうしても、コーナー部でビビってしまったが、スーパーG1チャックを活用すると、ビビリが一切なくなった。刃持ちが良くなり、切削条件も上げられるようになった」ことで、キタムラ機械のマイセンターや松浦機械のVXシリーズで展開している「大径工具での加工も、ミーリングチャックからスーパーG1チャックへと切り替えを図り、成果を上げてきている」と言う。
- 活用しているスーパーG1チャックは17本に及ぶ。
- 数量ベースで成果を表して頂くと「小ロットでの使用のため、算出が難しい」としながらも「1個当たり、加工時間が12時間から11時間に短縮し、刃物交換では3個で交換が5個まで対応できるようになった。刃物単価は2万円くらい」と試算してくれた。
- 博洋エンジニアリングでは、100分の1以内の公差に収めるのが基準であり「顧客が求める精度以上を常に追求している」(塚本工場長)。
- 面談の最後にユキワ精工への「要望」について聞いてみると「スラッジがこびり付いたりして、ねじ穴に不具合ができたりする。簡単に清掃できないものか。刃物の着脱や精度面に与える影響も、無視できないと思う」との感想が返ってきた。
突出し量を長くすることが求められている半導体関連の仕事でも、スーパーG1チャックならビビらない