メーカ的立場を志向し、強化するフジコー(福岡県・那珂川市)。ツーリングはユキワ精工製に集約へ。
スーパーG1チャック、ハイブリッドG1チャック、グリーンG1チャックと使い分け
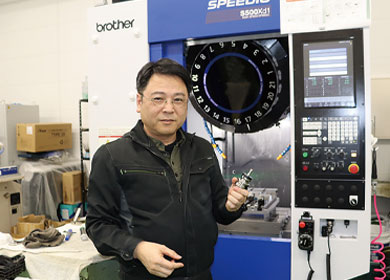
スーパーG1チャックを手に持つ秋山工場長
フジコーは、半導体や金型部品を扱う商社として1991年に創業した。
秋山工場長は「当初、受注した部品加工は協力工場に依頼し、顧客に納めていた。だが、その後、メーカー志向を強めるなか、10年後の2001年には、研削工程を担うべく工場を立ち上げ、2017年には研削の前後工程にも対応して、一貫生産の流れを構築した」と商社機能に留まらない、ものづくりへのシフトについて解説する。
現在の加工部門の仕事内容は、プリンターやカメラ、白物家電メーカーから依頼されたステンレス製装置部品(5割)ほか、パレットなどのアルミ製搬送部品(2割)、コンパックスやセラミックなどの脆性材(3割)の加工から成り、取引企業はおよそ60社に上る。
「一貫生産の流れのなかで、設備面では放電加工機からマシニングセンタへのリプレースが進んだ。時短に大きく貢献してくれたからで、ある事例では、9時間を要していた加工が1時間でできるようになった」。
だが、ある加工ではマシニングセンタの活用で課題を引きずっており、ユキワ製ツーリングとの出会いにも関連する、この現場を悩ませる加工があったのだ。
「ステンレス製装置部品で、φ16ミリに0+18ミクロンの公差穴に納める加工だった。ヘリカル加工を選択したが、精度安定には程遠く、とにかくバラツキが多くて困っていた」と言う。
求められる精度は、別言すればピンゲージにピタッと入れなければならないレベル。受注は、1ロット20個から30個で、求められる穴精度は同じだが、20種類と多い。
「現場で検討していたところ、加工方法ではなくツーリングを換えてみたら?と協力工場からアドバイスがあり、実績のあったユキワ精工製グリーンG1チャックと、大手ツーリングメーカーのものを比較検討。両者をキタムラ機械のマシニングセンタ(40番主軸)に搭載し、試したところ、2社ともに問題なく、加工ができたが、グリーンG1チャックの方が削れている音が良く、削った面もすっきりしていることから、ユキワ製ツーリングに軍配が上がった」。
この結果を踏まえて、昨年のブラザー工業製スピーディオ導入を機会に、ツーリングはすべてユキワ精工製を選ぶことになったようだ。
「昨年9月から稼働スタート。(条件がわかっている)リピート品は、スピーディオで対応し、φ1ミリ以下はハイブリッドG1チャック、φ8~φ12ではスーパーG1チャックと使い分けている」ほか「負荷のある加工は、40番主軸のキタムラ機械にグリーンG1チャックを組み合わせて対応している」。
ツール交換の際、以前はその脱着で不安を残したが「今はメガネレンチで締められるようになってきて安心できる」との感想も寄せられた。
フジコーでは現在、社内加工が1割、外注に9割の比重だが、今後とも、メーカー的立場を強化していく方針と言う。
困っていた公差穴の加工でテスト。加工音でユキワ製ツーリングを選定した
グリーンG1チャックを活用した部品加工例