リーマ加工での優位性に貢献するスーパーG1チャック。
刃具の交換時間短縮にも直結する成果出すロックミシンのパイオニア、鈴木製作所(山形市)
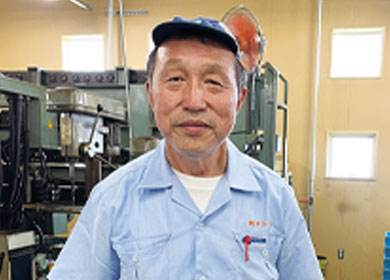
取材に対応して頂いた松田工場長
家庭用ロックミシンの製造で著名な山形市の鈴木製作所を訪問した。
松田工場長は「ロックミシンは布のほつれ止め用。布の厚さに関係なく自動調整し、裁断しながら縫うオートテンション機能、面倒な糸通しを解決したエアースルーシステムの採用が大きな特徴」と機能や性能を説明してくれた。
1968年に職人さんや家庭でも使える小型のロックミシン「ベビーロック」を世界で初めて開発。現在、国内4割、アメリカ・ドイツ・イギリス他、全世界向けに6割の比率で販売を展開している。
「ダイキャスト部材の切削加工が基本となる。加工では、段取り時間ゼロを追求し、様々な治具で対応を試みる一方、パレットプールを活用し、夜間運転にも配慮しながら、24時間稼働を目指している」。
コロナ特需が発生し、生産量が拡大、年産4万台~5万台ペースと言うのが昨年から今年にかけての実績。課題となるのが、残業を減らすため、いかに生産性を上げていくか。
「およそ3カ月先まで仕事が埋まり、予定が組まれているが、受注内容から、作り置きが可能な場合も多い。設備に求めるのはスピードで、時間当たりの出来高を上げて、海外勢との競争力で差をつけていきたいと考えている」。
好例として牧野フライス製作所、DMG森精機
スピード重視-その考えを織り込んで具体化したのが、2012年に検討した加工設備の老朽化更新時。DMG森精機「NH5000DCG」と牧野フライス製作所「a61nx」を導入し、生産開始。その後、牧野製同型機を2台、「a51nx」1台の追加導入へと結びつく(いずれも40番主軸の横形マシニングセンタ、すべてパレットプール付き)。ロックミシンのフレーム加工は横形マシニングセンタ、その他の多品種少量部品には立形マシニングセンタを活用している」。
スーパーG1チャックは、すでに100本近い保有量に
ユキワ精工のツーリングとの出会いは、およそ7年前。営業マン訪問時にスーパーG1チャックのテストサンプルを頂いたのがきっかけと言う。
「リーマ加工におけるチャッキング時の振れ精度で、他社製との違いを見せつけた。一度、クランプするだけで精度が安定し、刃具交換時間の短縮に直結。H6レベルの高精度を要する、リーマ加工を多用する際は100%活用している」ほか「ドリル加工は、長い突き出し量になる場合が多いが、スーパーG1チャックなら振れが無いため、1万回転以上で使用している」。
現場にはすでにスーパーG1チャックが100本近く活用されており、今後も増やしていく予定と言う。
「ユキワ精工のツーリングでは、12台ある自動旋盤にEYコレットを採用。シャフト物加工に24時間稼働させているが、低価格でありながら、加工精度が良くなり重宝している」との意見も聞かれた。
生産課の渡邊主任(左)と岸主任
実際のほつれ止め